Thermoplastic Injection Molding
The Process of Component Development
The process for creating a new injection molded component begins with the design and development of a functional concept. A 3D CAD model is created to determine the form and fit for the particular function that the component is designed to serve. Excel can provide design for manufacturability input to customers in the design phases of their molding projects to ensure that the designed components can be reliably produced to specification.
Once a part is designed, prototypes are created to confirm that the part will function as intended. Excel provides responsive, same day in-house 3D printing services to assist customers with their proof of concept.
Excel works closely with a number of mold makers to design injection molds that will consistently and efficiently produce components that meet specification. Considerations such as parting lines, draft angles, and gate locations are determined during this phase.
Upon completion of a new mold, all components are then fully validated utilizing the industry standard IQ/OQ/PQ approach. An initial parameter profile is developed utilizing Scientific Injection Molding principles. Further refinement of the initial process occurs during execution of Designs of Experiment (DOE). Proposed process control limits are then challenged though the Operational Qualification (OQ) portion of the validation. A Performance Qualification (PQ) is then performed to prove out the stability of the process under actual production conditions.
With the validations complete, parts are ready to be run for full scale commercial production. Excel has the capacity to mold routine production components in low and high volumes.
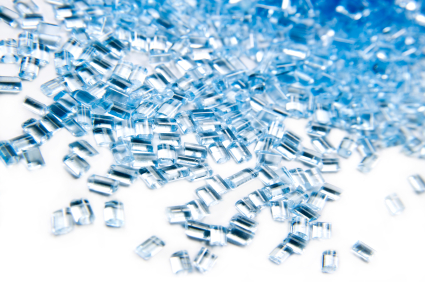